New smart barn platform and vertical fodder system go live
Plus, a new dairy data exchange organization emerges
The bar for launching new cow tech products continues to be set higher. The new gold standard it seems is to announce your latest offering in a live broadcast from a farm.
Earlier this year Lely announced its latest offerings from a farm in the Netherlands. This week another cow tech company announced its newest product live from a farm in the U.S.
Smart barn automates ventilation, lighting and cooling
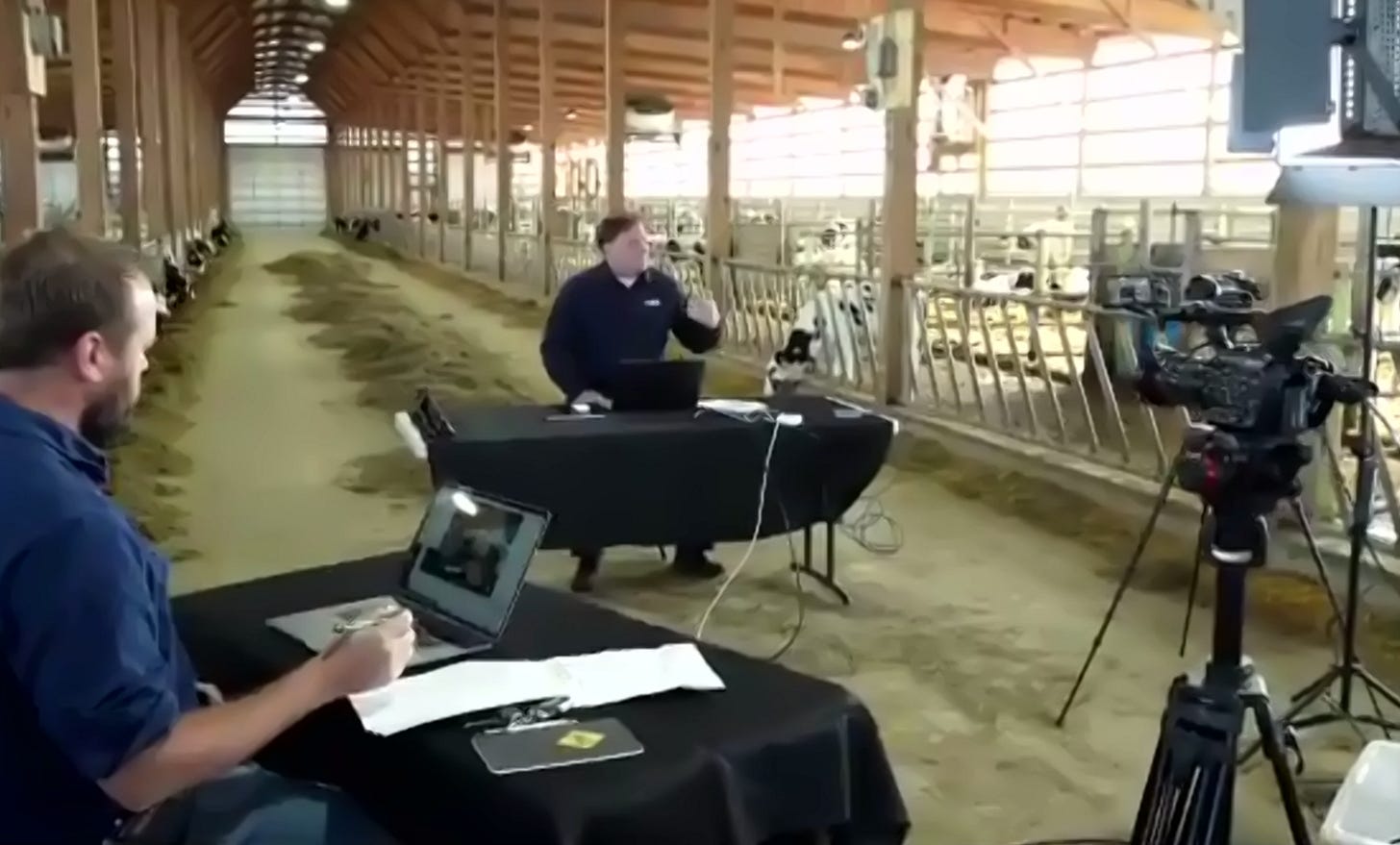
VES showcased its new smart barn control system, DairyBOS, in a live broadcast from Fetzer Farms in western Wisconsin. The facility is one of three beta sites for the now commercial product that provides full control and automation of any indoor cattle environment.
As an example of how the system works, if the temperature humidity index (THI) in a barn rises above a pre-set threshold, such as 68 THI, the system can increase air exchange by ramping up fan speed in order to move more air over cows and help to cool them. It can also control a barn’s lighting or the timing of other cooling methods, such as misting at the feedbunk.
While the system’s aim is to put any barn environment on autopilot, it can also be manually controlled, monitored or updated via an intuitive interface on a phone, table or computer with internet connectivity. The system keeps historical records of barn conditions and stores them indefinitely in the cloud.
“Sensors throughout the barn, connected fan feedback, as well as real-time weather information allows the system to adjust ventilation, lighting and cooling to ensure an environment that reduces instances of disease and lameness, and encourages comfort, rest and optimal feeding/producing conditions for each cow.” said Mark Doornink, the company’s vice president of product management.
The company claims the system will help reduce maintenance and repairs of fans or other barn environment components. That’s because the system suggests via alerts when a component that is not operating at efficiency may need attention. Also, the advantages of the system include a more consistent, documentable environment for cattle owners and downstream product buyers.
The smart barn system can be installed with the company’s products or added to existing systems that use competitors’ products.
“Gone are the days of a manager or supervisor having to walk around and check the buildings to see that systems are in operation,” Doornink said. “Now he or she has peace of mind and can verify that from a smartphone or tablet.”
New vertical, automated farm grows fodder for cattle
The second big launch this week occurred on a dairy farm in Utah. NuSkin-backed Grov Technologies unveiled a project it has been working on for several years – a vertical, automated growing and feeding system for grain-sprouted fodder.
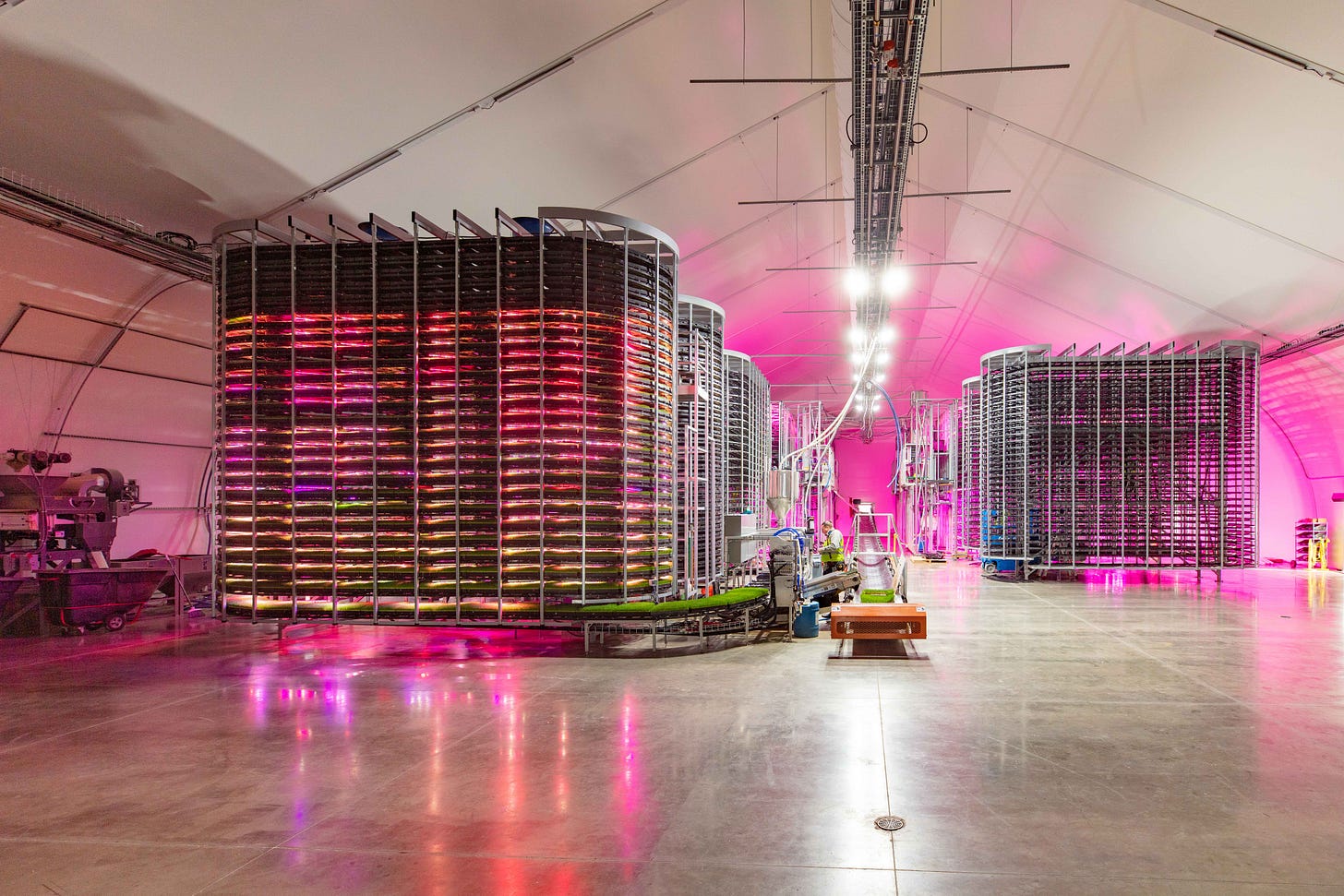
The new unit, named Olympus, takes up less than 900 square feet but can produce 5,000 to 6,000 pounds of sprouted wheat or barley grass per day. The vertical growing system can be linked together in an automated indoor farming system to grow fresh animal feed year round. The company claims its the largest such fodder system in the world.
“If you can get animals fresh; clean – no herbicides or pesticides; predictable; and optimized feed year-round and include that with the TMR , you'll improve the health of the animal. We’ve got data to show that you'll also improve feed efficiency,” said Steve Lindsey, president of Grov Technologies, to The Cow Tech Report in an exclusive interview prior to the product’s launch.
The technology stack that grows the fodder uses automation and robotics to optimize the growing environment, requiring only 5 percent of the water typically required for forage production. The system’s patented lighting emits specific light spectrums to grow feed with minimal electricity. The company has data to show that one automated vertical fodder farm can free up between 35 and 50 acres of traditional farm land – the acreage that would otherwise be required to grow a similar amount of feed.
The fodder’s 20 percent dry matter profile can replace 10 to 15 percent of a TMR’s ingredients. Just one of the automated growing towers can produce 1,100 pounds of fodder per day and feed 200 cows at a 6.5 pound inclusion rate.
In early feeding trials with 300 fresh cows, the fodder inclusion improved feed efficiency between 5 and 10 percent. The company has also trialed feeding the fodder to Holstein steers at up to a 35 percent inclusion rate. According to the company’s data, the beef market animals maintained or slightly improved their average daily gain while fed on the fodder diet.
“What is the narrative? It’s not just about feed efficiency, profitability or sustainability, but a better product for consumers,” Lindsey said.
Bateman Mosida Farms, where the pilot units have been growing fodder, has committed to feed up to 5,000 animals in 2021 using the company’s system.
Learn more here.
New dairy data exchange organization emerges
The International Dairy Data Exchange Network or iDDEN is the largest ever collaboration of data partnership in the dairy industry. It brings together milk recording organizations and national databases across 13 countries which represent 200,000 dairy herds and 20 million dairy cows. The platform aims to streamline data exchange among herds and between milk recording organizations.
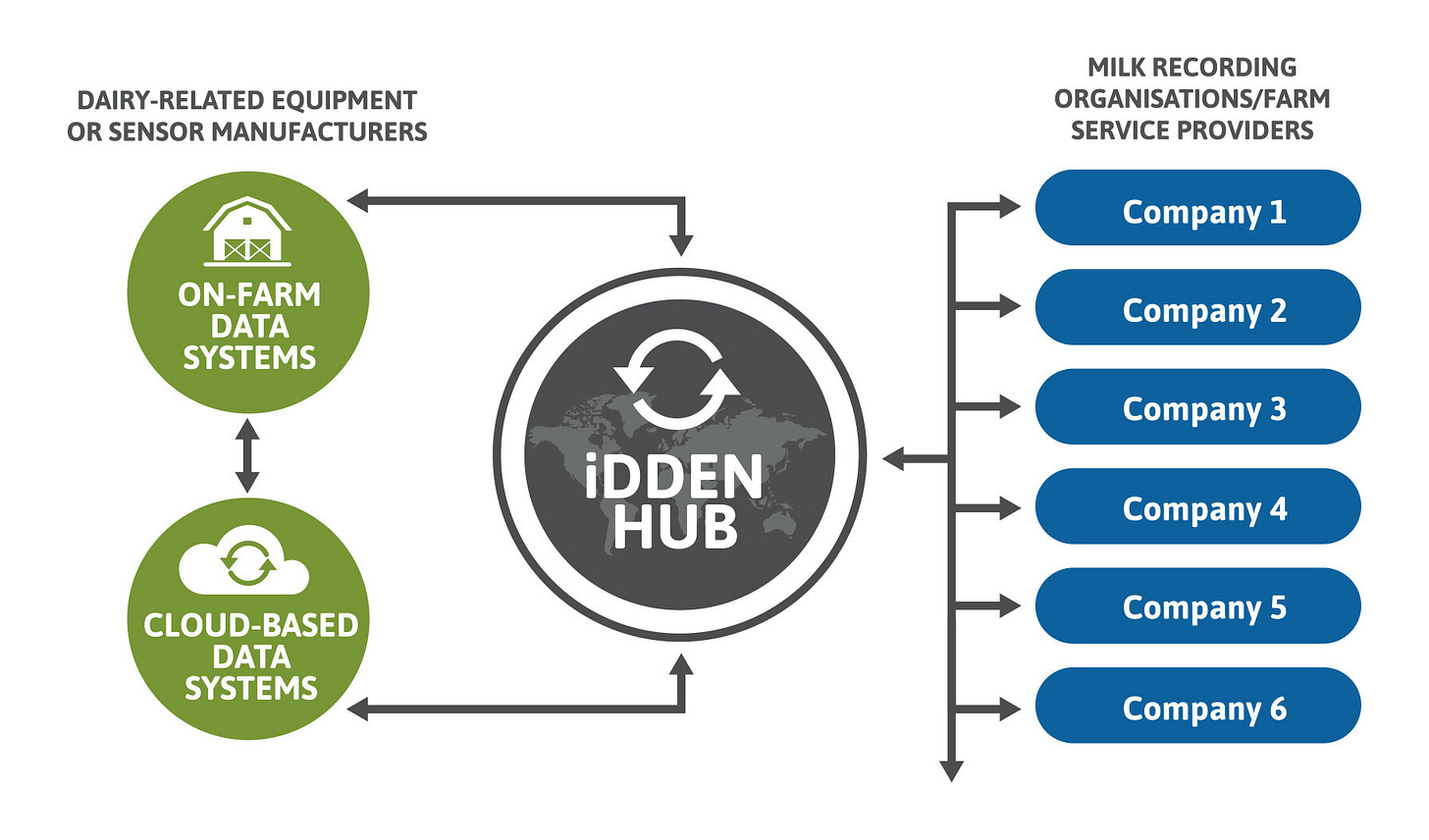
“iDDEN has the potential to reduce the costs of data integration by having one solution to connect multiple individual on-farm systems and dairy equipment data sources,” said Reinhard Reents, managing director of iDDEN.
The new exchange reassured dairy farmers on their website that they will “remain in control” of their data as they must authorize others to access it.
For more information, see the company’s website.
Parallel parlor milking robot video debuts on YouTube
MiRobot recently released a video showing how its parallel retrofit robotic milking technology cleans and pre-dips prior to milking. The video appears to be running at normal speed. If that is the case, the technology’s teat-spotting vision and performance speed appears slower than the cleaning and attach speeds in current box-milking robots.
Check it out for yourself.
In the news: RFID tags, processing meat with robots
Progressive Cattle magazine has an in-depth primer on the types of identification technology available for use in beef cattle. Low frequency and ultra-high frequency RFID tags are discussed. Read more here.
The magazine also has an interesting take on the feasibility of robotic meat processing in the U.S. Here’s an interesting line from the article:
“We’re in Silicon Valley regularly and talking with innovators nearly every month,” said one Cargill source about the company’s interest in robotic meat processing.
The article is worth a read.
Automated manure treatment system goes small-scale
Livestock Water Recycling recently announced a smaller version of its PLANT manure treatment system. According to the company’s announcement, the mini version – named SPROUT – can handle 1.1 to 2.6 million gallons of manure per year. CEO Karen Schuett told The Cow Tech Report that this new offering is more applicable to Canadian and European dairy markets, as well as U.S. farms in the Midwest and along the East Coast.
“It’s more accessible for 100 to 500 cows in a herd,” Schuett said.
The Canadian-based company believes the new product will help the company expand beyond its current U.S. footprint and offer other producers, especially those in its home country, something of interest.
You're not going to believe it … water skiing on a lagoon
If you’ve never seen anyone water ski on a lagoon, you’ve got to check out this video from BioFiltro. The company filters manure water physically and biologically using worms.
You won’t believe it until you see it, but watch to see the dairy owner do a full head-under-the-water dive.
Profit projections from ZISK
Projected profitability for two dairy herd sizes DECREASED
recently in profit projections from ZISK.
ZISK is a profit-projection smartphone app that tracks individual dairy farm profitability based on current CME board prices. Projections for a 1,000-cow dairy producing an average of 80 pounds of milk per cow and a 2,500-cow dairy producing an average of 85 pounds of milk per cow are provided.
12-month dairy farm profit projections (as of Nov. 12, 2020):
1,000-cow dairy = $371,700 (DOWN
about $170,000 in the last two weeks)
2,500-cow dairy = $2.07 million (DOWN
about $444,000 in the last two weeks)
Source: Zisk